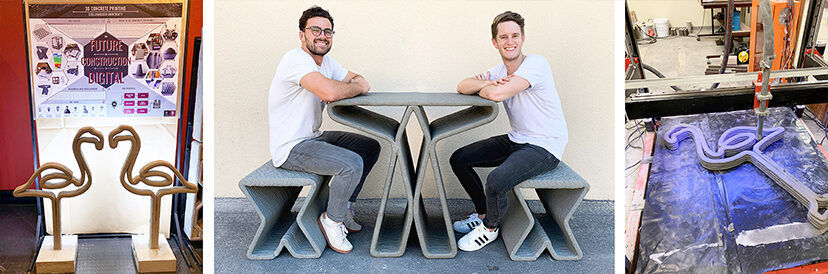
If you want to capture someone’s attention – display concrete flamingos! This strategy seems to have worked for two postgraduate students who exhibited their research in 3D printing of concrete at the SA Innovation Summit. “We received a very positive response from delegates at the Summit,” say Frederick Bester and Marchant van den Heever, postgraduate students in the Department of Civil Engineering. Frederick and Marchant were invited to exhibit their work at the SA Innovation Summit in Cape Town in September.
The Summit is in its 12th year and is an annual flagship event on the South African Innovation calendar. It was created to support and promote innovation, and nurtures, develops and showcases African innovation. It brings together corporates, thought leaders, inventors, entrepreneurs, academia and policymakers to try and increase South Africa’s competitive edge and to inspire sustained economic growth across the continent of Africa.
“Our exhibition attracted a lot of interest, especially from architects. It seems there is a great need for an aesthetic product that is easily available,” says Marchant. The good response could not only be attributed to the presence of the beautiful flamingos. Although it was logistically not possible or viable to demonstrate the actual 3D printing process in the small exhibition space at their disposal, they ably conveyed the impact of their research project by means of a poster, a video, a graphical presentation as well as interaction with visitors.
“3D printing of concrete promises to become a disruptive technology in the construction industry. It has the potential to reduce construction times and waste drastically, while also enhancing architectural freedom through its ability to produce geometrically-complex elements when compared to traditional methods of construction,” says Frederick.
The conventional approach to construction involves casting concrete into a mould (known as formwork) using materials such as timber. This formwork accounts for about 60% of the total cost of concrete construction and is a significant source of waste, as it is discarded. Worldwide the construction industry is responsible for 80% of waste and the formwork therefore not only adds to the cost of construction, but also contributes greatly to the waste. Another disadvantage of this conventional method is that pouring concrete into formwork limits the creativity of architects to build unique shapes, unless very high costs are paid for bespoke formwork. 3D printing utilises additive manufacturing techniques, which means objects are constructed by subsequent deposition of material layers. Free-form (using computer models) additive construction allows design freedom at no additional cost. The cost of producing a structural component would not be tied to the shape, so construction could be freed from the ‘ordinary and dull’ rectangular designs that are so familiar in current building architecture.
“If you want to enter the market, printing smaller items (such as these concrete flamingos) would be a good starting point,” says Marchant. Frederick adds jokingly: “If you want to make a ‘quick buck’ this is the way to go.” However, Marchant and Frederick have a much bigger picture in mind and are very serious about first completing their research and obtaining their PhD degrees. After that, there will be ample time to try and make a few ‘quick bucks’!
Frederick and Marchant are part of the diverse seven-member Stellenbosch 3D concrete printing team under the leadership of Prof Gideon van Zijl. The team’s research includes printable concrete material development, comprising foam concrete, high-performance standard and fibre reinforced concretes. In addition to research conducted on rheo-mechanical print process optimisation and durability assessment; the design and analysis of reinforcement strategies, prefabricated structural elements and the feasibility of 3D concrete printing in the South African context are investigated.
Photograph:
Main photograph: Marchant van den Heever (left) and Frederick Bester with the bench and table X-Furniture prototypes they manufactured by means of 3D printing of concrete.
Far right shows the 3D printing process of a concrete flamingo.
Far left are the elegant flamingos that attracted many visitors to the students’ exhibit at the SA Innovation Summit.