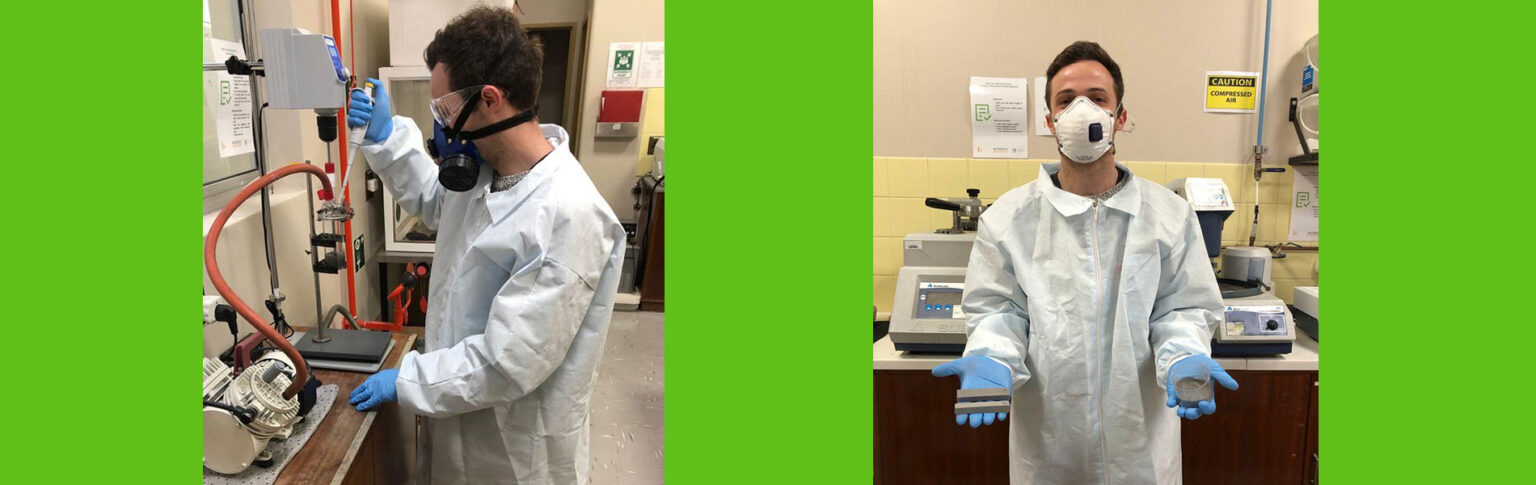
[Article by Nane Zietsman]
“I have always wondered what it would be like to be part of a new research area where there is no defined solution. The undergraduate experience shapes your intuition and understanding about the fundamental engineering principles, where postgraduate studies allow you the freedom to investigate the unknown.” This is how Wian Erasmus describes his postgraduate journey at Stellenbosch University.
Erasmus, who is currently pursuing his master’s degree in Mechanical Engineering, offers research on the gel-casting process of titanium powder. “I decided on this topic because I want to contribute research to the field of biomedical implants.” Erasmus is investigating this process as a cost and time-efficient manufacturing technique for producing complex shaped parts that require no melting or deformation of the raw material. He describes the process as follows: “A pourable solvent-powder mixture is created by mixing titanium powder with chemicals. This mixture then gets cast into a mould that resembles the final shape of the part. After the casting process, the solvent is removed by drying. The dried part is then placed into an oven to remove the chemicals. The final result is a sintered part that only consists of titanium.” In explaining his work, he uses the analogy of baking. “Ultimately, I am investigating and developing the recipe for gel-casting that can adequately produce defect-free parts.”
According to Erasmus, the COVID-19 pandemic had a considerable impact on his postgraduate experience. Being a type 1 diabetic, Erasmus had to take extra caution to ensure his health and safety when working on campus. “My biggest challenge was to manage my blood sugar levels when doing lab work. I work with dangerous chemicals and having a hypoglycaemic episode could put me at great risk.” Erasmus describes the Department as being very helpful in this regard. “They took note of when I needed to conduct lab work and checked up on me regularly.”
Despite his challenges, Erasmus remained dedicated to his work. He is excited about the contribution his research could make to the field. “If the recipe for the solvent-powder mixture is tweaked right, it can possess tremendous potential for the biomedical industry. By adjusting the combination and ratio of the ingredients, one can alter the mechanical properties of the parts. An example is the porosity of the parts.” According to Erasmus, various studies have been done on different gel-casting recipes to produce parts with a similar porosity to the human cortical bone. “If we can optimally refine this process, we will be able to make parts for implants to assist patients in a couple of days.”
Erasmus states that the results of his research so far look promising, and his supervisor, Prof. Deborah Blaine, requested him to submit an abstract of his study for the International Conference on Competitive Manufacturing (COMA). This conference presents recent developments, research results, and industrial experience related to Smart, Sustainable Manufacturing. COMA further acts as a generator for innovative ideas and fruitful collaboration both locally and abroad. This opportunity is one of the advantages of a master’s degree that Erasmus considered. “A postgraduate degree also allows you to network and share ideas with global experts in the field.”
Materials Engineering Research is one of the many postgraduate research themes that the Department of Mechanical and Mechatronic Engineering offers. Researchers in this group collaborate nationally and internationally with engineers and materials experts who are looking at innovative, sustainable, and resource-efficient ways to design new materials and new manufacturing processes that can be used to create functional, customised items. A core aspect of this research is uncovering the link between processing properties. Erasmus’s research is a prime example of the innovative engineering that students in this field can look forward to.
For more information on Mechanical and Mechatronic Engineering postgraduate offerings, visit: www.mecheng.sun.ac.za.
Photograph left: The setup of the experiment used for mixing commercially pure titanium gel-casting slurry in a GlassChem mixing vessel under vacuum conditions.
Photograph right: The gel-casting process that Erasmus is developing is a net-shape manufacturing process: it starts with titanium powder as raw material (as shown in the beaker in his left hand) and results in a cast green part (the two bars in his right hand) after 24hrs. No mechanical deformation or melting of the metal is required. Further sintering heat treatment, below the melting temperature, creates a solid titanium part in the as-cast shape.