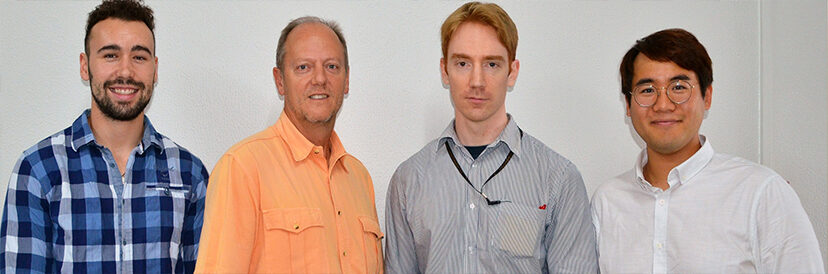
The first industrial-grade gantry type 3D concrete printer in Africa produced its first 3D printed object last month. Jacques Kruger, who recently upgraded to PhD in structural engineering, designed and manufactured the printer. The laboratory size printer with outer dimensions 1.3 x 1.3 x 1.67 m (w x l x h) has a build volume of roughly 1m3. Paired with a powerful 3-phase pump, the printer is capable of extruding a vast range of materials with varying rheology. This enables the research team to produce large structural specimens (walls, beams and columns) for testing, ultimately contributing towards fundamental research in the 3D printing of concrete (3DPC) industry.
The research team’s current main focus is on the development and characterisation of advanced cement-based materials suitable for 3D printing. In particular, lightweight foam concrete (LWFC) and nano-concrete (concrete infused with nanomaterials) are envisaged to yield the desired mechanical and durability characteristics. In the long term, the team aims to develop guidelines for the standardisation of structural design for 3DPC structures to ensure safe and durable 3D printed structures. Early reports indicate that 3DPC can significantly reduce construction times and waste, while also increasing architectural freedom and aesthetics through its ability to produce geometrically-complex structural elements. Through this project, the team endeavours to contribute to industrialisation and growth of the construction industry towards sustainable careers in the sector.
The 3DPC team at the Centre for Development of Sustainable Infrastructure (CDSI) under team leader Prof Gideon van Zijl, is Dr Stephan Zeranka (co-leader), Jacques Kruger, and Seung Cho (MEng student at the Department of Civil Engineering). Follow their progress on YouTube by clicking on THIS link.
Photo (from left to right): Jacques Kruger, Prof Gideon van Zijl, Dr Stephan Zeranka, and Seung Cho.